Frequency conversion cable solution
This product is applicable to the frequency conversion control system with AC rated voltage of 0.6/1kV and below as power supply cable or electrical connection. The product has strong resistance to voltage impact, can withstand the pulse voltage during frequency conversion, and the cable has good shielding, and can effectively eliminate electromagnetic interference, reduce the noise of frequency conversion motor, and ensure the stable operation of the system. It is widely used in metallurgy, electric power, petrochemical and other industries.
Electrical breakdown of insulation After a large number of variable-frequency motors have been used, general power cables, such as PVC insulated, sheathed cables or cross-linked polyethylene insulated PVC sheathed cables, are selected in most cases. Due to the high withstand voltage level of the cables, cable body breakdown rarely occurs. Why can the cable run for a long time under power frequency and break down within a few hours under frequency conversion? This is by no means an aging problem, which can be basically attributed to the impact of high-frequency pulse voltage. In general, PVC insulation is not ideal for land use because of its large dielectric loss. The XLPE insulation is satisfactory, and it has excellent properties such as organic, electrical and thermal properties. The insulation thickness of the cable can adopt the provisions of 1kV voltage grade. If it is thickened properly, it is certainly more reliable, which is more beneficial to the frequency conversion cable.
Although there is no national standard to regulate the assessment index of environmental pollution caused by electromagnetic waves emitted by cables, it is necessary to suppress external high-frequency interference. For a four core low-voltage cable, the first step is to improve the arrangement of insulated cores. If the four cores of the cable are directly cabled, it is an asymmetric structure. If the fourth core is decomposed into three insulated cores with smaller cross sections, and the three large and three small cores are symmetrically cabled, the symmetrical type is more favorable compared with the two cases. Second, it should be considered more important to strengthen the overall shielding structure. Manufacturers are used to using copper wire braiding for shielding. In fact, this is not a good method. The material consumption is large, the processing speed is slow, and the shielding effect is not ideal. It is an advanced structure and process to use copper strip to cover longitudinally and roll lines, forming a fully enclosed metal layer. As long as the thickness is appropriate, it can achieve effective shielding function. However, this process and the materials it uses are very common in the field of optical cables. The thickness of the copper strip should not be too thin to ensure the suppression of electromagnetic wave emission.
Grounding measures for the shielding layer Good grounding of the shielding layer is a necessary condition to suppress the external emission of electromagnetic waves. The grounding method of copper wire braided shielding is easy to solve, while the longitudinal wrapped copper strip corrugated shielding needs to be grounded with a special fixture. The contact surface of the fixture and the corrugated copper pipe should be consistent, and the grounding wire should be led out from the end of the fixture.
Outer sheath This kind of cable is mostly laid indoors, and generally does not need armor. Although PVC sheath is not completely excluded, high-density polyethylene is more appropriate
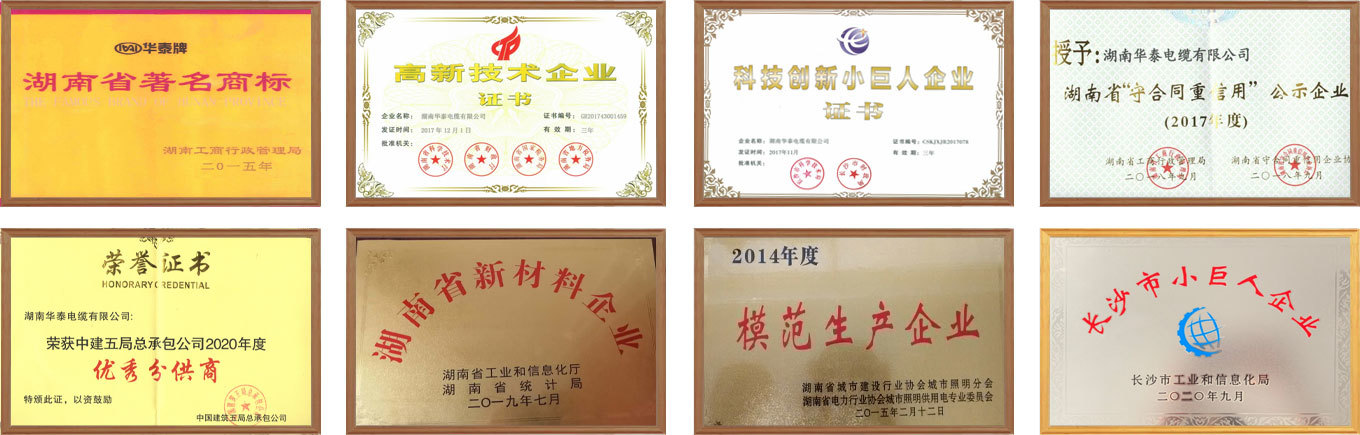